![]() |
![]() |
![]() |
![]() |
Egg packing production line consists of two sections:
1. Pulp processing section
2. Molding and drying section
The production line uses recycled paper and cardboard as raw materials and it can produce various types of egg packages.
There's one set of moulds for 30 cavities egg tray.
If it is required to produce egg-box,(tray with cover) it is necessary to have need another set of molds
Productivity - 1200 trays/hr (30 eggs in a tray)
1.Pulp recycling section
This proposal is for producing B,C grade toilet tissue. The raw material is waste paper. So we adopt the following machines.
(1) Waste paper deinking and production line | |
Waste paper →High consistency hydra-pulper→High consistency pulp pump→High level box→Vibrating screen→ 1#pulp pool→Floating and deinking machine with square cell→2#pulp pool→Thickener→№3 Pulp pool →Cleaning and refining machine→Bleaching drum Pressure screen →№4& Pulp pool →Pump →Pulp pool №5. | |
(1.2) High consistency hydra-pulperZGS3: 2SETS | |
Volume
|
3M³
|
Productivity
|
9-12TPD
|
Concentration of pulp |
12±2%
|
Diameter of container
|
Ø1800mm
|
Diameter of impeller
|
Ø 680mm
|
Impeller speed
|
400rpm
|
Inlet diameter
|
Ø 200mm
|
Diameter of diluting inlet
|
Ø 80mm
|
Equipped motor
|
Y280M-6/55KW
|
(2) High consistency pulp pump ZBGKS-150: 2SETS
Flow capacity
|
200M³/H
|
Delivery lift
|
18M
|
Speed
|
1000rpm
|
Diameter of outlet
|
Ø 150mm
|
Eqipped motor
|
Y180L-4/22KW
|
(3) 40M³ Pulp pool : 7 sets
Volume
|
40M³
|
Сonsistency of pulp
|
5%
|
Mixer type
|
Impelling type Ø 700
|
Eqipped motor
|
Y160L-6/11KW
|
Flow capacity
|
70M³/H
|
Delivery lift
|
18M
|
Speed
|
1440rpm
|
Eqipped motor
|
Y132M-4/7.5KW
|
(5) 0.9M² High frequency vibration screen ZSK1.8: 1SET
Flow capacity
|
20-40TPD
|
Screening area
|
1.8M²
|
Screening board specification
|
1080mm*2100mm
|
Diameter
|
ø3mm
|
Vibration frequency
|
1440times/min
|
Input pulp concentration
|
2.5%
|
Output pulp concentration
|
2%
|
Amplitude
|
4-5mm
|
Eqipped motor
|
Y132S-4/5.5KW
|
Capacity
|
<30TPD
|
Floating consistency
|
1-1.3%
|
Inputting pressure
|
0.1-0.2
|
Outputting pressure
|
DN100
|
Diameter of outlet
|
300*600
|
Blow off diameter
|
DN100
|
Admitting pipe diameter
|
11/2’’
|
Air bubble generater motor
|
Y100L2-4/2.2KW
|
Scraper motor
|
0.37KW
|
Diluting water inlet
|
DN50
|
Speed of scraper
|
40rpm
|
Input pulp consistency
|
1%
|
Outputting pulp consistency
|
5%
|
Roll-thread pressure
|
10N/cm
|
Filtering area
|
10M²
|
Drum board width
|
2020mm
|
Drum speed
|
1.5-15rpm
|
Roll diameter
|
ø460mm
|
Roll width
|
2141mm
|
Pulp inlet diameter
|
DN300mm
|
Pulp outlet diameter
|
DN250mm
|
WHite water outlet diameter
|
DN250mm
|
Eqipped motor
|
YCTG180-4A/5.5KW
|
(8)Cleaning and refining machine ZSLC-50N:
Flow capacity
|
25-30TPD
|
Pulp inputting consistency
|
2-5%
|
Inputting pressure
|
0.1-0.2MPa
|
Eqipped motor
|
Y200L2-2/37KW
|
( 9) 50M³ bleaching drum ZPC700: 2SETS
Volume pulp pool
|
50M³
|
Сonsistency of pulp
|
6%
|
Impeller diameter
|
700mm
|
Impeller speed
|
750rpm
|
Eqipped motor
|
Y160L-6/15KW
|
Bleaching drum specification
|
ø1500*1300 2 sets
|
Speed of bleaching drum
|
12rpm
|
Eqipped motor
|
Y100L1-4/2.2KW
|
(10) 0.5M² pressure screen: 1SET
Slotted screen
|
0.25mm
|
Сonsistency of pulp
|
2-4%
|
Flow capacity
|
25-35TPD
|
Inlet diameter
|
ø200mm
|
Outlet diameter
|
ø200mm
|
Scumming pipe diameter
|
Ø80mm
|
Pressure of inlet
|
0.1-0.2Mpa
|
Eqipped motor
|
Y225S-4/37KW
|
Flow capacity
|
200M³/H
|
Delivery lift
|
20M
|
Speed
|
2900rpm
|
Engine power
|
18.5KW
|
(12) White water pump IS150-125-250: 1SET
Flow capacity
|
22M³/H
|
![]() Set of tanks for pulping section |
![]() Full set of tanks for pulp section |
![]() Foam pump |
![]() Pulp pool |
![]() Engines of the pulp section (solid, explosion-proof frames) |
![]() Desinfection and bleaching system |
![]() High consistency pulp pump ZBGKS-150 |
Foundation, adjustment and alignment
Raw materials
(1) The paper pulp moulding production line uses the quite pure waste paper generally;only includes a few sand dusts, the adhesive tape,plastic overlay,and so on impurity. For example: Waste book newspaper, waste kraft paper, waste corrugated paper board bits and pieces, printing paper bits and pieces, waste carton and so on. The fibre of this kind of waste paper is very good, the paper pulp growth rate is high, only pulping by the hydraulic pulper then achieved the paper pulp moulding production line operation requirement, the latter working procedure does not need to complex screening, purgation processing. Because the paper pulp moulding production line does not look like the papermaking equipment, Relatively, it consumed the paper quantity is less, if the used waste paper raw material is disorderly and dirtied serious low-grade waste paper, then the pulping system needs to establish complex screening、purgation processing equipment; This for such situation which consumes lowness of paper quantity of the paper pulp moulding produc-tion line, is inappropriate, because the fibre quality of low-grade waste paper is bad, the paper pulp growth rate is low, the performance and outward appearance of the roll out of product is bad, the cost of screening purgation processing is high, the invests of equipment is big, consump-tion power is high, operation complex; synthesize the raw material cost not to be lower than the use pure waste paper cost. General, The commonly used waste paper fixings is: the 20%-30% waste book newspaper add the 80%-70% waste corrugated paper, may according to the user’s waste paper raw material nature to adjust.
(2) The function of the disperse type emulsified gum rosin water-repellent lets the product have the waterproof performance, cannot because meet the water to decompose immediately
(3) AL2 (SO4)3 is the flocculant, It function is to help to disperse type emulsified gum rosin water-repellent adsorption on the paper pulp fibre and enhance the water-repellent function effect.
(4) Other chemical for example: The defoamer, the helps filters intensifier and so on, may according to the user’s waste paper raw materials nature to increase again, does not use generally. In the summer, in the weather burning hot situation, after adding the disperse type emulsified gum rosin water-repellent to the preparation pulp pool, maybe produce a considerable of froths, only this time it is necessary to use the defoamer, it may be substituted by some petroleum of industrial used, for example: Diesel oil.
2. Molding and drying section
Power demands:
- Water 0.5-1 ton/hr
-Power 380 V, 50 HZ, 75 kW
- Diesel oil 15-20 kg/hr
Installation requirments :
- Working place - (30-40) х (8-12) х (4-5) meters
- Finished products warehous ; 150 m2 and more
Workers/shift : 4-7 persons.
2.1. A list of equipment for ZMG-B4 supplied by the seller
No. | Name | Amount | Units. | Notes |
I | Pulping system | |||
1 | ZDS1.5m3 hydraulic pulper | 1 | unit. | Contains electric motor |
2 | Pulp pump ZJB-A | 1 | unit. | Pulp pump of hydraulic pulper |
3 | Pulp pump YW80-29-9 | 1 | pc. | Loses the pulping to pump |
4 | Pulp pool stirrer | 2 | pc. | Own trademark |
5 | Filter cell | 1 | pc. | Trademark |
6 | White water pump | 2 | pc. | |
II | ZMG-B4 type forming machine | 1 | pc. | size: 1600×540, the PLC micro-computer control, the rotary sys-tem forming way |
III | Auxiliaries system of forming machine | |||
1 | Vacuum pump SK-6 (limit vacuum degree:-0. 093Mpa) | 1 | set | |
2 | Air-water separator (vacuum tank) | 1 | set | Including fluid position control system |
3 | Dehydration pump | 1 | pc. | Imported bearing, stainless steel roller, hard alloy mechani-cal seal. |
IV | Drier DW1.6X18 (with automatic drying belt | 1 | set | Effectively heats up the area 1.6 meters ×18 meters, divides 2 sec-tions, Brings the natural gas hot-blast stove itself to heat up |
V | Semiautomatic hot-pressing reshap-ing machine :QZX-3T type | 1 | pc. | Platen size: 900×450 electric heating, semiautomatic movement |
VI | Control system of electrical equipment | 1 | set | Control apparatus of production line and second power cable. |
VII | Pulp pipe, valve | 1 | set | Exclusive to fraction of pulping system and forming machine sys-tem of the production line |
VIII | Spare parts of one year | 1 | set | |
IX | Forming molds | According to the contract requirements | ||
X | Heating and pressing moulds | According to the contract requiremen |
Drying chamber
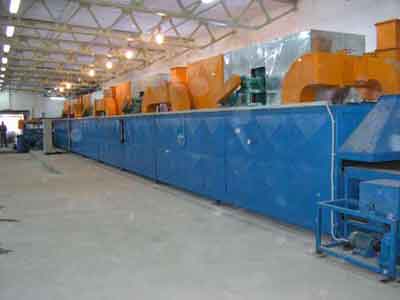
![]() Drying chamber being installed |
![]() Assembled drying chamber |
The DW1.6X18 type straight burn mode fuel natural gas drier of the ZMG-B4 type auto-matic paper pulp moulding production line, it use the natural gas to supply heat power; it use the natural gas burner is made in Italy and use the natural gas valve-group is made in Germany, they are utterly very safety and trustiness. Otherwise, the control system of the drier has setting the safety safeguard system; it only the all of the lead blowers for expel the damp have be running, so that the natural gas burner could be start running and burning. The conveyer belt motor of drier is used frequency adjust equipment to adjust the speed having no caste, so it has the inte-grated safeguard function. The waterish products which made in from forming machine have the water content: 70%~75%, and they be transferred in to the conveyer belt of drier by the transfer moulds of forming machine, and moving with the conveyer belt. The waterish products which into the drier will be dried and expelled the water by the circulatory hot wind system of drier, and to arrive at dryness degree request. The drier use the unique wind way system, so it let the products to be distortion very small when they after be dried. So that, when produces the normal egg tray, the fruit tray, the industrial product packing, they only need to be dried to the end product directly; When pro-duces the high quality egg box, the fruit tray, the high quality industrial product packing, the wa-terish product to be dried to the technology requirement dryness degree, retention definite mois-ture, then carry on the working procedure of hot- pressing reshaping, attain to the requirement of the end product B.The operation instruction of the drier.
1) The Inspections and preparative of the drier before start-up to running.
Inspect if the natural gas fountain supply is normal, Inspect if natural gas pipe, valve, instrument is normal, if has find the problem please obviate problem immediately.Inspect if the every transmission parts is all right, if some tightening screw had loosed, if has found the problem please obviate problem immediately.Inspect if the lubricating oil quantity of the gear speed reducer is normal, if every transmission parts is lubricated all right, give the lubricating oil to the parts which need distance time to append lubricating oil. Switch on the electric fountain, start the fan blowers、lead blowers and drier conveyer belt frequency adjust equipment, let they running about 1~2 minute, look into if blowers and conveyer belt running normal, if have unconventionality please stop running and to inspect or refer the problem to maintenance man to obviate. After affirm the natural gas fountain supply、electric system and transmission parts were running normal, it is possible to start running the drier.
2)Open the electric control tank operation panel door, and close the switch QF0, give the electric control tank of drier the total electric fountain, the voltmeter should show: 380V. Get the electric fountain switch in the operation panel (“power supply”key switch) to close, then give the drier electric control system the control electric fountain, the electric fountain pilot lamp will light. After electric fountain “ON”, 1#、2#temperature control instrument will respec-tively show the 1#、2#drier current temperature. Turn the temperature control instruments “lower limit temperature---show--- upper limit temperature” function transi-tion switch on “lower limit temperature” place, and turn the lower limit temperature adjusting knob to the number which is needed; Turn the function transition switch on “upper limit temperature” place, and turn the upper limit temperature adjusting knob to the number which is needed; then Turn the function transition switch on “show” place, so that the upper and lower limit temperature bound to be setting complete. The concrete temperature bound should be set for every segment drier may be ascertain according as the actual production instance; normally the first segment set for: 165 ℃ ~170 ℃, the second segment set for: 160 ℃~165 ℃ After setting the temperature, one by one to press the “1#、2#Blower ON” button switch every distant 1~2 minute、that the opposite“1#、2#、Blower running beacon” light. When 2 sets fan blowers be started and running one by one, please pay attention to if they have unconventionality, and if their running electric current normally. After the 2 sets fan blowers running normally, one by one to press the “1#、2#、Exhaust fan ON” button switch every distant 1 minute、that the opposite“1#、2#Exhaust fan beacon” light. When 2 sets lead blowers be started and running one by one, please pay at-tention to if they have unconventionality. After the 2 sets fan blowers and 2 sets lead blowers have be running normally, turn the “Gas burner total OFF---ON” knob switch to “ON” place, that the “Gas burner total beacon ” pilot lamp light, and the 2 sets fuel natural gas burners could be allow to start. When this time, if any one of the 2 sets lead blowers has not be running, that the “Gas burner total beacon ”pi-lot lamp not light, but the “Gas burner total alarm” pilot lamp to light and sound an alarm, that any one of the 2 sets burners will could not to start; This is a safety safeguard function. After the “Gas burner total OFF---ON” has be start normally, one by one to turn the “1#、2#Gas burner OFF---ON” knob switch to “ON” place; At this time, the 2 sets fuel natural gas burners will respectively controlled by opposite temperature control instru-ment. When the temperature of the opposite drier is lower then the“lower limit temperature” number, the temperature control instrument control the burner to ignition and burning, then to heat the drier. When the temperature of the opposite drier is overstep the “upper limit temperature”, the temperature control instrument control the burner to stop ignition and burning, then to stop heat the drier, and the temperature of drier will not rise. So that before start to producing, in the drier box need to be heated and rise the temperature, when produce the products the drier box will keep the temperature bound. After the drier box has be warmed-up arrive the temperature bound which had be setted, start the drier conveyer belt to running. Adjust the speed of conveyer belt according to the production technologic request, besides the conveyer belt speed should matches the speed of the forming machine work cycle. The electric control parts of conveyer belt had be installed into the forming machine electric control tank, so that could let the operator to adjust the speed of conveyer belt expediently. The concrete operation is: press the “frequency adjust equipment power ON” button switch, that the “frequency adjust equipment power beacon” light, so the frequency adjust equipment of drier has be given the electric fountain. Turn the “drier conveyer forward---reverse” knob switch to “forward” place, and press the “drier conveyer RUN---STOP” two place button switch to “RUN” place, that the frequency adjust equipment input the forward direction electric fountain to the conveyer belt motor, adjust the frequency knob switch which in the control panel of frequency adjust equipment to adjust the frequency, then to adjust the rotate speed of conveyer belt motor, and then to adjust the speed of conveyer belt. Reseat the “drier conveyer RUN---STOP” two place button switch to “STOP” place, the frequency adjust equipment stop to input the forward direction electric fountain to the conveyer belt motor, the conveyer belt will stop to running. The conveyer belt could be choosed the forward or reverse runnig according to the actual request. If the conveyer belt motor is over loading、the voltage too lower、in defect of electric fountain each other , that the frequency adjust equipment will close automatically then to make safety safeguard function; And stop to output, switch off the electric fountain, to show the cause of malfunction; and to let the “drier conveyer breakdown alarm” pilot lamp to light and sound an alarm. After the drier box has be warmed-up arrive the temperature bound which had be setted, and the conveyer belt of drier has be running and be adjust all right, that could start the forming machine to produce the produce, and put the waterish products into the drier to be drying. Re the detailed control and adjust means of the production course, please read the “ control means of production course”.
3)When need to finish the production, the drier need to be stopped according to de-pict detailedly hereinafter: First, one by one to turn the “1#、2#Gas burner OFF---ON” knob switch to “OFF” place, the 2 sets fuel natural gas burners will to stop running. b. Reseat the “drier conveyer RUN---STOP” two place button switch to “STOP” place, the frequency adjust equipment stop to output the electric fountain, the conveyer belt stop to running. press the “frequency adjust equipment power OFF” button switch, get the input electric fountain to be switched off. Despite the 2 sets burners had be stop running, but the temperature of the fuel natural gas hot-wind stove and drier box are very high, so that the fan blowers and lead blowers need to be continued running for period of time, and open up the new wind opening; then get the hot-wind stove and drier box to be cooled. Normally, after the temperature of in the drier box had be cooled lower than 80℃ ~100 ℃, they are all right; At that time, the temperature of in the hot-wind stove had be lower too. If had’nt got the hot-wind stove and drier box to be cooled, that the remaining heat in the hot-wind stove will bring the heat exchange to the hot-wind stove steel shell, then let the temperature of the hot-wind stove steel shell to rise very high, so that the temperature of fuel natural gas burner will rise very high too. If the burners suffer the high temperature chronically, that they will mangle possibly. After the temperature of the drier has be depressed, that could stop the fan blowers and lead blowers to running, and keep the new wind opening to open up, so that the drier has be stopped right. If the distant times of “stop running” is long or distant one day to produce again, that the switch QF0 must to be switched off, and to off the natural gas supply valve.
4)The detailed control and adjust means of the production course
Inspect if the water content of the product which had be dried were accord with the produc-tion technologic request, and to adjust. If the water content is more, that step up the setting temperature of in the drier box; or lower the speed of drier conveyer belt, then to continue the time of drying. If the water content is too little, that lower the setting temperature of in the drier box, or step up the speed of drier conveyer belt, then to curtail the time of drying. If the water content difference of the production upside and underside was very more, that adjust the throttle of upper and under wind line pipe of drier, then to change proportion-ment of upper and under wind line pipe to gush wind. Normally, the gushed hot-wind quantity of upper wind line pipe should to be adjusted to more than the under wind line pipe, because the hot-wind gushed will all rise and up to the roof of drier box; moreover, the gush wind hole of upper wind line pipe to the production is far then the under wind line pipe to the production; so that if the gushed hot-wind quantity of upper wind line pipe is more, that the hot-wind speed gushed will fast more and the distance of hot-wind will far more. When produce the productions, the first drier segment is the segment for get the water-ish products to warmed-up and step up the temperature; in there the evaporation is very little, so the new wind opening of the hot-wind stove and the expel wet opening should be adjusted to small, and to use the circulatory hot-wind mainly. In the two segment drier boxes, the evaporation of produces is very more, and the humidity is very high; so that the new wind opening of the hot-wind stove and the expel wet opening should be adjusted to big; Then reinforce the new wind more, and get the plentiful damp ex-pelled outside, lower the humidity to in favor of drying.
The technology parameter of the drier
The box (namely is effective dry area) of DW1.6X18 type straight burn mode fuel natural gas drier had be compartmentalized to 2 segment, every segment length is: 9 M, total length is18 M, The box width is: 1.96 M, height is: 1.85 M.
Every segment box of drier has equip one set straight burn mode natural gas hot-wind stove.
The primary technic parameter of drier is:
Total dimensions | Length:18000×Width:2360×Height:3100(mm) |
The figuration dimension of every segment drier box | Length:9000×Width:1960×Height:1850(mm) |
The effective dry area of drier | Length:18000×Width:1600(mm) |
Temperature of the drier | It compartmentalized into 2segments, each segment all may alone set and control tem-perature. the first segment set for: 165 ℃ ~170 ℃, the second segment set for: 160 ℃~165 ℃ |
Drier conveyer belt running speed | 0.5M~6M/Min, use frequency adjust equipment to adjust the speed having no caste. |
The heat way of the drier | The drier itself bring straight burn type natural gas hot-wind stove |
The burner of drier | RIELLO 40-GS20” burner made in Italy, natural gas valve-group “MBDLE407BO1” is made in Germany. |
Quantity of heat Supplied by natural gas hot-wind stove | every set supplie 100 000~150000kcal/h, and could to be adjusted |
Drier drying power | Each hour dry dehydration volume is 400~450kg. |
The total power of drier | 37.4 KW 37.4KW |
Demand of natural gas pressure adjustment valve | 200~500mmH2O, 2~5Kpa |
Diameter of the Indoor every one byway pipe to supply natural gas | Every natural gas burner need 3/4”(Dg20) or more |
Volume of supply natural gas | Every burner needs 20~25M3/h. |
Heat quantity of natural gas | 8000~8500 kcal/m3 |
Actual fuel quantity of natural gas for pro-duction | 45~60m3/hr |
Hot pressing reshaping machine
Hot press![]() |
Hot press being mounted ![]() |
The brief introduction of Semiautomatic pneumatic hot-pressing reshaping machine
Our company produces the QZX-3Ttype Semiautomatic pneumatic hot-pressing reshaping machine is improves in the original 1 type foundation, it not only absorbed 1 type structure to be architectonic, Services conveniently, the power consumed is low, efficiency is high; Moreover with 1 type compares, because it let the under mould move out to meets the produce, therefore the operator did not need to let the hand to enter between the hot-pressing formwork to carry on the operation, eliminated the danger which is possibly appeared crushes the hand when the operator carry on the operation. Let the operator to be safer, felt relieved. Because QZX-3T type Semiautomatic pneumatic hot-pressing reshaping machine be de-signed to architectonic, therefore uses the great diameter and short itinerary air cylinder to pres-surize, gathers the mould press to be possible to achieve above 3 tons, so it could made the pro-duces very widely. Compares with the hydraulic pressure reshaping machine, The QZX-3T type Semiautomatic pneumatic hot-pressing reshaping machine has been short set of hydraulic units, the use and the maintenance convenient. Compares with the pressure reshaping machine which uses the great diameter and long itinerary air cylinder to pressurizes, the airs consumption is small, saves the power. In the QZX-3T type Semiautomatic pneumatic hot-pressing reshaping machine, every hot-pressing formwork uses 6 the electric heat stainless tubes to heat up tempera-ture, each electric heat stainless tubes power: 0.8KW, the efficiency of heats up is high, the hot-pressing formwork will heat up quick to the temperature on which will request, moreover it will renew conveniently.
The operation instruction of Semiautomatic pneumatic hot-pressing reshaping machine
In order to guarantee the operator safety and does not damage the equipment and the mould, if new machine begins the production for the first time, after the equipment service to begins the production; and after constantly between stops using to begins the production, the equipment must carry on the debugging after the below step to be normal , only then begins the production
Preparatory work
1. Inspections all pipelines do connect, the vacuum pump and the air compressor work whether normally, pressure in may use in the scope. Air operated part pressure: 0.4Mpa ~ 0.6Mpa,Vacuum degree: - 0.06Mpa ~ -0.08Mpa.
2. Inspect in the hot-pressing reshaping machine frequently, if the locknut of chain joint had be loosely which attach the up formwork and air cylinder, and promptly screws tight locked, Prevented crashes the up formwork to damage
3. Frequently inspect if locknut of chain joint had be tight locked which attach the under formwork and move air cylinder. Inspects if the shock absorber locator of under formwork had be adjusted and be screws tight
4. Inspect power sources line dose connect normally, the changeover switch is at the manual condition
Opening machine without moulds to debugging machine
1.Turn off the power source, Inspect electromagnetic induction switch and so on various parts are whether normal
2. Manual debugging each air operated parts and air cylinder movement is whether norma
3. Transfer hot-pressing reshaping machine to be in the automatic movement original state, namely the up formwork to be in the upper limit position, gets the under formwork to be in the front limit position; at this point in the two positions the obverse electromagnetic induction switch’s lamp should shine.
4. Let the changeover switch allocate move in the automatic running status, depress the automatic movement button, hot-pressing reshaping machine should according to the below step movement
(1) Three position and five interface electromagnetisms valve YV2a attracts gathers, The piston rod of cylinder to shrink which could move the under formwork, gets the under formwork to be in the hind limit position, at this point, the lamp of electromagnetic induction switch which be in the under formwork’s hind limit position must to be bright.
(2) Three position and five interface electromagnetisms valve YV1b attracts gathers, The big cylinder piston rod stretches out, the up formwork moves to the under limit position, namely the position of gather the mould to pressurize. At this point, the lamp of electromagnetic induction switch which be in the up formwork’s under limit position must to be bright.
(3) After waited some time for gathers the mould to pressurize (user could adjustment the clock relay “KT1” to intercalate the time for gathers mould to pressurize, the clock relay is in the front keyboard), three position and five interface electromagnetisms valve YV1b release, YV1a attracts gathers, Electromagnetism cross valve commutation, The big cylinder piston rod shrinks, up formwork upward movement; at the same time, two position and five interface electromag-netisms valve YV3 attracts gathers, it control under formwork’s air operated cutoff valve for blow air to opens, get the under formwork to blow air. Two position and five interface electro-magnetisms valve YV4 attracts gathers, it control up formwork’s air operated cutoff valve for inbreath to opens, the up formwork inbreath. This movement process function is shifts the prod-uct from under mould to up mould, ready for the up mould into next step to blow air to decline the produce. While up formwork rise, Works as the inductive bonce away from area of electro-magnetic induction switch (Namely when the lamp of electromagnetic induction switch be in the under limits dose black out), The under formwork stops blow air .
(4) As the up formwork moves to the upper limit position, the upper limit position electromagnetic induction switch lamp to be bright. Three position and five interface electromagnetisms valve YV1a release, and it return to inbetween position function, up formwork stops in the upper limit position. Then Three position and five interface electromagnetisms valve YV2a release, YV2b attracts gathers, electromagnetism cross valve commutation, the piston rod of cylinder for move under formwork stretch out, the under formwork move.
(5) After the under formwork moves in front, it stop at front position. At the same time, the front limit position electromagnetic induction switch lamp to be bright, tow position and five interface electromagnetisms valve YV4 release, it control up formwork’s air operated cutoff valve for inbreath to closure, tow position and five interface electromagnetisms valve YV5 attracts gathers, it control under formwork’s air operated cutoff valve for blow air to opens, up formwork blow air, After delay some time the up formwork stop blow air. The delay time could be intercalate by adjust the clock delay “KT2” which is in the electrical control chest. Above is a hot-pressing reshaping machine movement cycle, the user should test many times, after confirmed the movement is unmistakable only then could installs the mould. When installing the mould, certainly must electrify, Open into the compressed air. Use the “manual condition” to control the under formwork move to be in the hind limit position, let the up formwork rises to the upper limit position, Then put the moulds. Into hot-pressing form-work, Uses the clamps to suppress the under moulds first, then use the “manual condition” to control the upper formwork move down, and suppress the up moulds with the clamp. Like this installation, the hot-pressing reshaping moulds to be used will not be abrade and break, because between up an under moulds the location is accurate. Before install the hot-pressing reshaping moulds, must get the location of between up and under moulds to accurately; generally it May use putting in the product to locate. When install the moulds certainly must pay attention to the security. Strictly prohibits to start various pneumatic parts when the operator’s hands enter be-tween the up and under formwork to install the moulds, In order to avoid mistaken operation which could has the accident.
Production operation
1. First closehot-pressing reshaping moulds by manual operation way, start the electric heating of up and under formwork, heat up the hot-pressing reshaping moulds to the intercalative temperature. According to a variety of hot-pressing reshaping moulds shape, and according to the water content of produce different, the temperature of hot-pressing reshaping moulds could be adjusted and intercalated between 120 ℃ —170 ℃ . When the temperature be intercalated, the upper limit and lower limit temperature difference is: 5 ℃ —10℃.
2. After the hot-pressing reshaping moulds heats up arrive at intercalative temperature, get the changeover switch from the manual condition to automatic condition, then carries on the production operation. The operator must complete the certain protective measure, wear thin work glove and the arm protective covering, in order to avoid in burnt by hot-pressing reshaping moulds.
3. If the products had distorted very more in front of the hot-pressing reshaping, then will be supposed to adjusted the distortion place by manual way in front of the hot-pressing reshaping. If the products too dry (namely water content too low in front of the water content) , then needs to spray the water mist, enhances the water content. If the water content of products to be too more in front of the hot-pressing reshaping, then needs let the products to be dry air, to removes part of moisture, reduces the water content. Re the becoming water content of products in front of hot-pressing reshaping, it could be adjusted and determined by the way of trial run. According to a variety of produces shape is different, and a variety of produces facade smooth finish after hot-pressing reshaping is different, so the water content need be adjusted and determined between: 30%-15%. If the water content had be determined in front of hot-pressing reshaping, so the drier movement parameter may be determined. When continuous production, the water content of produces after be dried is almost same, only a few products appear too dry, or too wet, or the distortion is too more; according to the above method to process then, by this way, it could enhance the rate of finished products of hot-pressing reshaping working procedure.
4. Concrete production operations process The operator standing in front of the hot-pressing reshaping machine, and smoothly put the produces into the under hot-pressing reshaping moulds which will moving outside and stay there, as then presses down the automatic operation start button conveniently, The hot-pressing reshap-ing machine will automatically complete: The under hot-pressing reshaping moulds returns to move → the up hot-pressing reshaping moulds move down to gather the mould to pressurize → pressurizes produces spend number second → up hot-pressing reshaping moulds rise with pro-duces to separate the up and under moulds →under hot-pressing reshaping moulds continue to move outside and stay there to meet produces , and Carries on the repetition above movement process → at the same time, the up hot-pressing reshaping moulds will blow down the produces from the up hot-pressing reshaping moulds to the meet board which moving with under hot-pressing reshaping moulds to enters in the hot-pressing reshaping machine. The produces at meet board to be taken away regularly by the porter. The entire movement process all controlled by the electricity to work automatically, the worker only must put the produces into the under moulds which move outside and stay there, and presses down the button then. Therefore this add the spot apply oil working efficiency is high, The labor intensity is low, The security is ex-tremely good.
Working instruction
1. Regularly add the lubricating oil for the hot-pressing reshaping machine, the air-water separator of air-fount treater must turn on the water frequently; The oil mist implements must timely supplement the lubricating oil, guarantee it can drop and mist lubricating oil to lubricate air operated part.
2. When the hot-pressing reshaping machine be working, strictly prohibits let the hand entering the formwork or between other movement parts to do any work. After has start hot-pressing reshaping machine to automatically working, if discovered the equipment has abnormal or has the foreign matte in the hot-pressing reshaping moulds, even if can damage the machine, mould, either product, but does not allow get the hand to enter between the formwork or other movement parts to does any adjustment work; This time should promptly press down button of "urgently stops" to stop the machine movement; Then chooses the manual condition to process problems.
3. When the equipment appear the breakdown, should commit it to the specialized serviceman of equipment to process problems, in order to avoid the person and the equipment receive the injury.
Breakdown treatment and regulation of Semiautomatic pneumatic hot-pressing reshaping machine
Normally, The hot-pressing reshaping machine will not appear the breakdown. In the entire movement process of hot-pressing reshaping machine, if which step has appeared the breakdown, please according to following way to treatment and regulate.
1. Hot-pressing reshaping machine can not work after press down the button of “ automatic start”.
a. Inspect if the changeover switch has been changed from at the “manual condition” to at “automatic condition
b. Inspect if the up formwork to be in the upper limit position, and the under formwork to be in the front limit position; in the two positions the obverse electromagnetic induction switch’s lamp should be shine; If they all shine, so should inspect if the relay of the electromagnetic induction switch has attracted gathers, If they not attract gathers, so the obverse electromagnetic induction switch was broken, please replace.
c. If according to “a, b” way to inspect, they all normally, so please inspect if the electro-magnetisms valve YV2-a is normal, if the air pressure and other air operated parts is normal, if the mechanical has be stuck
2. After press down the button of “ automatic start”, the under formwork move to be hind position, but the up formwork cannot move down
a. Inspect if the under formwork has moved to be in the hind limit position, and if the obverse electromagnetic induction switch’s lamp shine, if the obverse relay “KA3” of the electro-magnetic induction switch has attracts gathers.
b. Inspect if the electromagnetisms valve YV1--b is normal,if the air pressure and other air-operated parts is normal, if the mechanical has be stuck
3. After up formwork move down, it stop in the under position, hot-pressing reshaping machine cannot carry on movement Inspect if the up formwork move down to be in the under limit position, and if the obverse electromagnetic induction switch’s lamp and relay “KA2” working normal
b. Inspect if the hot-pressing reshaping clock relay “KT1” in the front keyboard working normal.
c. Inspect if the electromagnetisms valve YV1--a is normal, if the air pressure and other air operated parts is normal, if the mechanical has be stuck
(4).When the up formwork rise, the under formwork can not blow air, and the up formwork can not inbreath.
a. Inspect if the reducing valve “14” and the blow air pipe ball valve of under formwork had be opened, if the valve YV3 and air operated cutoff valve “10” for under formwork to blow air had be working. If they had be broken, please replace.
b. Inspect if the inbreath pipe ball valve of up formwork had been opened, if the valve YV3 and air operated cutoff valve “16” for under formwork to inbreath had be working, If they had be broken, please replace.
(5).After the up formwork rise to the up position, it stop in there and can not carry on move-ment.
a. Inspect if the up formwork rise to the up limit position, if the obverse electromagnetic in-duction switch’s lamp and relay “KA4” working normal.
b. Inspect if the valve YV2-b normal, and if the air pressure and other air operated parts is normal, if the mechanical has be stuck.
(6).After the up formwork rise to the up limit position, and under formwork move outside, but up formwork can not blow air to decline the produces.
a. Inspect if the under formwork move to the front limit position, if the obverse electromag-netic induction switch’s lamp and relay “KA1” working normal.
b. Inspect if the blow air pipe ball valve of up formwork had be opened, if the valve YV5 and air operated cutoff valve “15” for under formwork to blow air had be working, If they had be broken, please replace.
c. Inspect if the clock delay “KT2” for up formwork to blow air working normal which is in the electrical control chest. Above is the problem which could appeared in the hot-pressing reshaping machine move-ment process, and the obverse way for breakdown treatment. If couldn’t except the breakdown according to the Above way , please inspect if the electrical system have breakdown, If the elec-trical parts had be broken, please replace. In the production process, if appears the problem which will impinge on the produces qual-ity and consecutive production, must carry obverse reglage into effect.
(1)If after the produces had be hot-pressing reshaping, but the paries fat not even, and the produces facade smooth finish not even.
a. Inspect if the moulds installation have aberration, so that must to adjust.
b. Inspect if the shock absorber locator of under formwork had be loosened, so the location was not accurate. so that must to adjust
c. Inspect if the platemark fluting razorblade was contorted and Buckled, so the location of moulds was not accurate, so that must to adjust
(2)If after the produces had be hot-pressing reshaping, but the produces facade smooth finish not very good
a. Inspect if the pressure of the cylinder for up formwork was to low, so that must to adjust.
b. Inspect if the produces too dry, so that need to adjust.
c. If the products had distorted very more in front of the hot-pressing reshaping, so need to adjusted the distortion place by manual way in front of the hot-pressing reshaping.
d. Inspect if the temperature of moulds had be intercalated too low.
(3)When be in hot-pressing reshaping, the produces could’nt be shifted from under mould to up mould very favourably.
a. Inspect if the inbreath of up moulds and blow air of under moulds working normal, if the amount of inbreath and blow air too low, and to adjust.
b. Inspect if the aperture of the up and under moulds had be back up.
c. Inspect if the water content too more before hot-pressing reshaping.
d. Inspect if the temperature of moulds had be intercalated too low, and the time of hot-pressing reshaping had be intercalated too few.